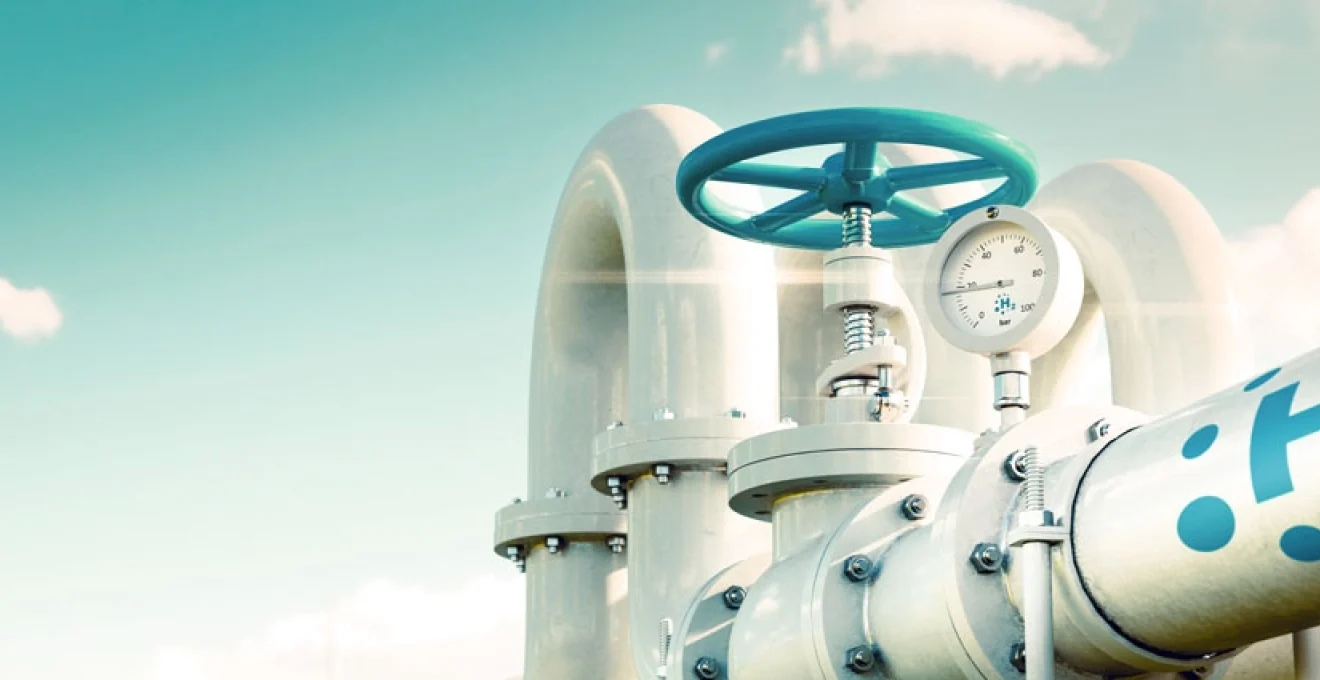
Hydrogen energy represents one of the most promising pathways toward decarbonizing our global energy systems. As a versatile energy carrier with zero direct emissions when used, hydrogen offers unique advantages across multiple sectors from transportation to industrial applications. The growing momentum behind hydrogen technologies stems from their ability to complement intermittent renewable energy sources, provide long-duration energy storage, and offer solutions for hard-to-abate sectors where direct electrification proves challenging. With global climate targets requiring rapid transitions away from fossil fuels, hydrogen-based solutions are emerging as critical components of a sustainable energy future.
Recent technological breakthroughs have dramatically accelerated the viability of hydrogen as a mainstream energy solution. Innovations in production methods, storage technologies, and end-use applications are converging to create unprecedented opportunities for large-scale deployment. While challenges remain around cost reduction, infrastructure development, and policy frameworks, the trajectory points toward hydrogen playing a central role in clean energy transitions worldwide. The adaptability of hydrogen across diverse applications makes it particularly valuable in creating integrated energy systems that maximize efficiency and minimize environmental impact.
Hydrogen production technologies for sustainable energy generation
The production of hydrogen represents the foundation of any hydrogen energy system, with several competing technologies offering different pathways to clean hydrogen. Currently, global hydrogen production is dominated by fossil fuel-based processes that generate significant carbon emissions. However, alternative production methods utilizing renewable electricity, biomass, or advanced thermochemical processes are rapidly maturing to offer genuinely sustainable options. The environmental impact of hydrogen depends entirely on its production method, with color-coding systems now widely used to differentiate between green (renewable-powered), blue (fossil-based with carbon capture), gray (conventional fossil-based), and other production pathways.
The technological landscape for sustainable hydrogen production continues to evolve rapidly, with dramatic cost reductions expected throughout this decade. According to recent industry analyses, the cost of electrolytic hydrogen is projected to decrease by 50-70% by 2030 as electrolyzer technologies scale up and renewable electricity costs continue to fall. This economic transformation is being accelerated by both technological innovation and policy support, creating the conditions for hydrogen to compete directly with fossil fuels across multiple applications. The diversity of production pathways also offers important flexibility, allowing regions to leverage their specific renewable resources and industrial capabilities.
Green hydrogen via electrolysis: advanced PEM technology
Green hydrogen production through electrolysis represents the gold standard for truly sustainable hydrogen energy systems. This process uses renewable electricity to split water molecules into hydrogen and oxygen with zero carbon emissions. Proton Exchange Membrane (PEM) electrolyzers have emerged as leading technologies in this space, offering compact designs, rapid response capabilities, and high efficiency.
The rapid response characteristics of PEM electrolyzers make them particularly well-suited for integration with fluctuating renewable energy sources. Unlike earlier alkaline electrolyzers, modern PEM systems can ramp output up and down within seconds, allowing them to follow the variable generation profiles of wind and solar installations. This dynamic operation capability enables “green hydrogen” production that maximizes the utilization of renewable electricity without requiring constant baseload power.
The material science underpinning PEM electrolyzers continues to advance, with innovations focused on reducing the platinum group metal content of catalysts while improving durability and performance. These systems can operate at current densities above 2 A/cm², significantly reducing the physical footprint and capital cost of large-scale installations. The modular nature of these systems also enables rapid scaling, with multiple units able to be combined into hydrogen production facilities ranging from megawatts to gigawatts in capacity.
Blue hydrogen production methods: steam methane reforming with carbon capture
Blue hydrogen offers a transitional pathway toward decarbonization by combining conventional production methods with carbon capture and storage (CCS) technologies. The predominant approach involves steam methane reforming (SMR) of natural gas, paired with systems that capture CO₂ emissions before they enter the atmosphere.
The technical architecture of modern blue hydrogen facilities incorporates multiple capture points to maximize carbon sequestration. Post-combustion capture systems extract CO₂ from flue gases using advanced amine-based solvents, while pre-combustion pathways convert natural gas to synthesis gas and separate the carbon before combustion. The captured carbon is then compressed, transported, and sequestered in geological formations, completing the carbon management cycle.
While blue hydrogen still relies on fossil gas as a feedstock, the dramatic reduction in associated emissions makes it a vital bridge technology while fully renewable hydrogen systems scale up. The International Energy Agency estimates that blue hydrogen can achieve lifecycle emissions reductions of 80-90% compared to conventional hydrogen production, providing immediate climate benefits. For regions with established natural gas infrastructure and geological storage capacity, blue hydrogen offers a pragmatic near-term solution that leverages existing industrial capabilities while supporting the longer-term transition to completely renewable hydrogen systems.
Biomass gasification for hydrogen: syngas production techniques using miscanthus and switchgrass
Biomass gasification represents a renewable pathway to hydrogen production that leverages organic feedstocks rather than fossil resources. This thermochemical process converts biomass materials into synthesis gas (syngas) – a mixture primarily containing hydrogen, carbon monoxide, and carbon dioxide – which can then be further processed to isolate hydrogen. Purpose-grown energy crops like Miscanthus and switchgrass offer particularly promising feedstocks due to their high yields, minimal input requirements, and carbon sequestration capabilities during growth. These perennial grasses can produce up to 25 tons of biomass per hectare annually while requiring minimal fertilization and growing on marginal lands unsuitable for food production.
The gasification process typically occurs at temperatures between 700-1200°C in the presence of controlled amounts of oxygen and/or steam. Under these conditions, the complex organic molecules in biomass break down into simpler gaseous compounds. The resulting syngas undergoes water-gas shift reactions to convert carbon monoxide and water into additional hydrogen and carbon dioxide, maximizing hydrogen yield. Advanced reactor designs incorporating fluidized bed technologies enable efficient processing of variable biomass feedstocks while minimizing tar formation and other operational challenges traditionally associated with biomass gasification.
From a sustainability perspective, biomass-derived hydrogen offers significant advantages when the entire lifecycle is considered. When managed properly, energy crops like Miscanthus and switchgrass sequester carbon in their root systems and soil, potentially creating a negative-carbon pathway to hydrogen production. Research at several universities has demonstrated that these perennial grasses can increase soil carbon by 0.5-1.5 tons per hectare annually while simultaneously producing biomass for energy conversion. This carbon sequestration, combined with the displacement of fossil-based hydrogen, creates a powerful climate mitigation double-benefit that few other energy technologies can match.
Solar-driven hydrogen: photoelectrochemical systems and stanford’s artificial leaf technology
Photoelectrochemical (PEC) hydrogen production represents one of the most elegant approaches to clean hydrogen, directly converting sunlight to hydrogen through specialized semiconductor systems. Unlike conventional electrolysis that requires separate solar panels and electrolyzers, PEC systems integrate light harvesting and water splitting into a single device. Stanford University’s artificial leaf technology exemplifies this approach, using advanced nanomaterials to mimic the photosynthetic processes found in nature. These systems typically employ semiconductor photoelectrodes immersed in water that generate electric current when illuminated, driving the water-splitting reaction without external power inputs.
The theoretical efficiency advantages of integrated PEC systems are substantial, with the potential to achieve solar-to-hydrogen conversion efficiencies exceeding 15% – significantly higher than separate photovoltaic-electrolyzer configurations. Stanford’s artificial leaf incorporates a tandem photoelectrode architecture that harvests different portions of the solar spectrum, maximizing energy capture across wavelengths. The photoelectrodes are coated with specialized catalyst materials that lower the activation energy required for hydrogen and oxygen evolution reactions, further improving system performance.
While PEC hydrogen production remains primarily in the research and development phase, recent breakthroughs in materials science and nanofabrication are accelerating its path to commercialization. Challenges being addressed include long-term stability in aqueous environments, cost-effective manufacturing techniques, and scaling from laboratory demonstrations to commercial systems. The development of earth-abundant catalysts to replace scarce platinum-group metals represents another active research direction. If these technical hurdles can be overcome, direct solar-to-hydrogen systems could eventually provide one of the most straightforward and efficient pathways to renewable hydrogen production.
Thermochemical water splitting: Sulfur-Iodine and hybrid sulfur cycles
Thermochemical water splitting offers an alternative route to hydrogen production that utilizes high-temperature heat sources rather than electricity to drive the decomposition of water molecules. Among various thermochemical approaches, the Sulfur-Iodine (S-I) cycle developed stands out for its theoretical efficiency and potential for large-scale implementation. This closed-loop process involves a series of chemical reactions that ultimately split water into hydrogen and oxygen without direct electrolysis, offering potential efficiency advantages in settings where high-temperature heat sources like nuclear, concentrated solar, or industrial waste heat are available.
The S-I cycle operates through three main chemical reactions. First, water reacts with iodine and sulfur dioxide to produce hydrogen iodide and sulfuric acid. These compounds are then separated and decomposed through the application of heat at different temperature levels (approximately 450°C for hydrogen iodide and 850°C for sulfuric acid). The decomposition reactions release hydrogen and oxygen respectively, while regenerating the iodine and sulfur dioxide for reuse in the cycle. This closed-loop nature means the process consumes only water and heat while producing hydrogen and oxygen, with all other chemicals being continuously recycled within the system.
Hydrogen storage and distribution infrastructure
The development of robust storage and distribution systems represents one of the most critical challenges for the hydrogen economy. Unlike conventional fuels with established infrastructure, hydrogen requires specialized solutions due to its physical and chemical properties. With the lowest density of any gas and a tendency to cause embrittlement in certain materials, hydrogen necessitates purpose-designed storage vessels, transportation systems, and handling protocols. Despite these challenges, rapid advances in materials science and engineering are yielding increasingly efficient and economical solutions for hydrogen containment and delivery.
The infrastructure requirements for hydrogen vary significantly depending on end-use applications and geographic context. Industrial hydrogen users typically require large volumes delivered via dedicated pipelines or produced on-site, while transportation applications need distributed refueling networks with high-pressure storage. Emerging residential and commercial applications may utilize lower-pressure hydrogen blended into existing natural gas networks or delivered via specialized distribution systems. Each pathway presents unique technical and economic challenges, creating a complex landscape for infrastructure developers. According to research from the Hydrogen Council, global investment in hydrogen infrastructure is projected to reach $300 billion by 2030, reflecting the scale of development required to support growing hydrogen adoption across sectors.
Strategic planning for hydrogen infrastructure increasingly focuses on the development of “hydrogen valleys” or clusters where production, storage, distribution, and multiple end-uses are co-located to maximize efficiency and minimize initial investment requirements. These integrated hydrogen ecosystems allow infrastructure to develop incrementally, with each component supporting the others to overcome the classic “chicken-and-egg” dilemma of matching supply and demand growth. As the hydrogen economy expands, standardization of key components such as connectors, safety protocols, and quality specifications will be essential to ensure interoperability across regions and use cases. Visit eo-dev.com for more insights on energy infrastructure development approaches.
Pipeline infrastructure: FutureGrid H100 project and BlendH2 standards for natural gas networks
Pipeline transportation represents the most efficient method for large-scale, continuous hydrogen delivery, particularly within industrial clusters or densely populated regions. The FutureGrid H100 project in the United Kingdom exemplifies the emerging approach to purpose-built hydrogen pipeline networks. This pioneering initiative aims to establish the first 100% hydrogen gas network in a real-world setting, repurposing existing natural gas pipelines where possible and installing purpose-built hydrogen lines where necessary. The project incorporates advanced materials resistant to hydrogen embrittlement, specialized compression systems, and enhanced leak detection technologies designed specifically for hydrogen service. The phased approach first demonstrates hydrogen delivery to residential customers at the neighborhood scale, with plans to expand to industrial users and larger geographic areas as the technology proves successful.
In parallel with dedicated hydrogen pipeline development, significant work is underway to establish standards for blending hydrogen into existing natural gas infrastructure. The BlendH2 standardization initiative brings together utilities, regulators, and equipment manufacturers to determine safe and practical hydrogen concentration limits for various segments of natural gas systems. Current research indicates that many existing pipelines can accommodate hydrogen blends of 5-20% by volume without significant modifications, potentially offering a transitional pathway that leverages trillions of dollars of installed infrastructure. Critical considerations include the impact of hydrogen on pipeline materials, compressor stations, end-use appliances, and safety systems.
The economics of pipeline hydrogen transport improve dramatically with scale and utilization. Analysis from the European Hydrogen Backbone initiative suggests that repurposed natural gas pipelines can transport hydrogen at costs between €0.10-0.15 per kilogram per 1000 kilometers – significantly lower than alternative transport modes. This economic advantage increases as networks expand and connect multiple production sites with diverse consumers, creating the foundation for liquid hydrogen markets. The development of standardized technical specifications for “hydrogen-ready” pipeline components is further accelerating this transition, with manufacturers now producing valves, compressors, and monitoring systems designed for future hydrogen compatibility.
Fuel cell applications across industrial sectors
Fuel cell technologies are increasingly penetrating diverse industrial sectors, offering unique advantages over conventional power systems in many applications. Unlike batteries or combustion engines, fuel cells generate electricity through an electrochemical reaction between hydrogen and oxygen, producing only water and heat as byproducts. This clean operation, combined with high efficiency and excellent scalability, makes fuel cells particularly valuable in applications ranging from portable power to stationary generation and transportation. The modular nature of fuel cell systems also provides important flexibility, allowing installations to be precisely sized to application requirements and expanded incrementally as demands grow.
The market diversification of fuel cell technologies has accelerated dramatically in recent years, driven by improved durability, reduced costs, and growing demand for zero-emission power solutions. According to industry analyses, the global fuel cell market is projected to grow at a compound annual rate exceeding 25% through 2030, with installed capacity increasing from approximately 1.5 GW in 2022 to over 15 GW by the end of the decade. This growth spans multiple sectors, with particularly strong momentum in material handling, backup power systems, data centers, and heavy-duty transportation applications where the rapid refueling and high energy density of hydrogen fuel cells offer distinct advantages over battery alternatives.
Technological innovation continues to enhance fuel cell performance while driving costs down. Advanced manufacturing techniques, reduced platinum loadings, increased power densities, and extended operational lifetimes have collectively improved the value proposition of fuel cell systems across applications. The development of specialized fuel cell architectures optimized for different operational profiles – from constant baseload power to dynamic load-following – further extends their range of applications. As production volumes increase and supply chains mature, the Department of Energy estimates that automotive fuel cell system costs could decrease from current levels around $75/kW to below $30/kW by 2030, approaching cost parity with conventional powertrain technologies in many applications.
Solid oxide fuel cells (SOFC): bloom energy servers for grid-scale applications
Solid Oxide Fuel Cells (SOFC) operate at significantly higher temperatures (typically 600-900°C) than PEM systems, enabling efficient electricity generation with less stringent fuel purity requirements. Bloom Energy has pioneered commercial SOFC deployment with their Energy Server platform, which can generate electricity from hydrogen, natural gas, biogas, or blended fuels with electric efficiencies exceeding 60% – substantially higher than conventional combustion-based generation. The solid-state architecture of these systems eliminates moving parts in the power generation process, contributing to quiet operation and high reliability with expected operational lifetimes of 10-15 years in continuous service.
The modular design of Bloom’s systems enables deployment across a wide power spectrum, from 100 kW installations for commercial buildings to multi-megawatt arrays serving data centers and industrial facilities. Each server incorporates thousands of planar ceramic cells arranged in stacks and electrically connected to provide the desired output voltage. The high operating temperature creates valuable waste heat that can be captured for facility heating, absorption cooling, or industrial processes, potentially increasing total system efficiency to over 80% in combined heat and power configurations. Unlike most power generation technologies, SOFC systems maintain high efficiency even at partial loads, providing important flexibility for applications with variable demand profiles.
Recent advances in SOFC technology have dramatically improved durability while reducing manufacturing costs. Bloom’s implementation uses specialized zirconia-based ceramics that resist degradation at high temperatures, along with engineered support structures that accommodate thermal expansion cycles without compromising electrical connections. The high-temperature operation presents unique engineering challenges but enables the use of non-precious metal catalysts – typically nickel-based materials rather than platinum – significantly reducing material costs compared to low-temperature fuel cell architectures. As manufacturing processes mature and economies of scale increase, the company has reported consistent cost reductions approaching 15-20% for each doubling of cumulative production volume, establishing a clear pathway toward economic competitiveness with conventional generation across growing application segments.
Marine transport: ABB and ballard power’s MW-scale systems for deep-sea shipping
The maritime sector represents one of the most challenging transportation segments to decarbonize, with limited alternatives to conventional heavy fuel oil for long-distance shipping. ABB and Ballard Power Systems have formed a strategic partnership to develop megawatt-scale hydrogen fuel cell systems specifically engineered for marine applications, targeting vessel types from passenger ferries to container ships. Their collaborative approach integrates Ballard’s fuel cell expertise with ABB’s propulsion systems and maritime engineering capabilities, resulting in modular power solutions that can deliver 3+ MW of continuous power with dynamic load-following capabilities essential for marine operations. These systems have demonstrated resilience in demanding maritime environments, with enhanced tolerance for vibration, salt exposure, and variable ambient conditions.
The marine fuel cell architecture developed through this collaboration incorporates multiple redundant modules to ensure operational reliability, with each fuel cell stack capable of independent operation. This distributed design enables partial-system maintenance without complete power loss and provides inherent fault tolerance for mission-critical propulsion applications. The systems employ liquid cooling circuits that maintain optimal operating temperatures while facilitating heat recovery for vessel services. Advanced control systems continuously optimize performance across varying load profiles, from low-power maneuvering in port to sustained cruising power, achieving overall system efficiencies exceeding 55% from hydrogen to electrical output across typical operational cycles.
Practical implementation of hydrogen fuel cells in deep-sea shipping requires addressing the considerable challenges of onboard hydrogen storage for extended voyages. ABB and Ballard are exploring multiple pathways, including high-pressure gaseous storage for shorter routes, liquid hydrogen for medium-range applications, and chemical carriers like ammonia or methanol that can be reformed to hydrogen onboard for the longest voyages. The International Maritime Organization’s increasingly stringent emissions regulations provide significant regulatory drivers for this transition, with carbon intensity reduction targets of 40% by 2030 and 70% by 2050 creating a clear imperative for zero-emission propulsion technologies. Early deployments on passenger ferries and coastal vessels are establishing the operational experience and regulatory frameworks that will eventually enable broader adoption across the global shipping fleet.
Aviation applications: ZeroAvia’s hydrogen-electric powertrains for regional aircraft
Aviation presents unique challenges for decarbonization due to stringent weight constraints, safety requirements, and the need for high energy density fuels. ZeroAvia has emerged as a leader in developing hydrogen-electric propulsion specifically designed for aircraft applications, with a phased approach targeting progressively larger platforms. Their initial powertrains combine high-power density fuel cells with electric motors that directly drive propellers, eliminating the complexity and weight of intermediate gearboxes while achieving system-level power densities competitive with conventional turboprop engines. This architecture offers not only zero-emission operation but potentially reduced maintenance requirements and lower operating costs compared to traditional aviation powerplants.
The company’s technical roadmap demonstrates the scalability of their approach, beginning with 600kW systems for 9-19 seat regional aircraft and progressing to 2-5MW powertrains for 40-80 passenger commuter planes. Each generation incorporates lessons from previous implementations while pushing power density and specific energy boundaries. The latest systems achieve remarkable power-to-weight ratios exceeding 2 kW/kg at the powertrain level, approaching the performance metrics necessary for commercially viable regional aviation. Critical innovations include lightweight hydrogen storage tanks that optimize the balance between pressure, weight, and volumetric efficiency, along with sophisticated thermal management systems that maintain fuel cell performance across the wide temperature and pressure ranges experienced during flight operations.
Regulatory pathways for hydrogen aircraft are developing in parallel with the technology, with ZeroAvia working closely with aviation authorities to establish certification standards for hydrogen systems in airframes. Their approach focuses on retrofitting existing aircraft initially, which simplifies the certification process while providing operational validation in commercial settings. This strategy has attracted partnerships with major aerospace manufacturers and airlines, accelerating the path to market. According to industry analyses, hydrogen-electric propulsion could capture 30-40% of the regional aircraft market by 2035, with early commercial passenger services projected to begin by 2025. These developments represent a pivotal moment in aviation, offering the first truly scalable pathway to zero-emission flight for short and medium-haul air travel – a sector that has proven particularly difficult to decarbonize through other technologies.
Economic viability and market scaling of hydrogen technology
The economic landscape for hydrogen technologies is undergoing rapid transformation as production scales, technologies mature, and policy support mechanisms evolve. While hydrogen solutions have historically faced cost challenges compared to incumbent technologies, this gap is narrowing substantially through multiple parallel developments. Manufacturing scale-up, technological learning curves, increasing carbon pricing, and dedicated hydrogen support mechanisms are collectively improving the business case across the value chain. According to recent analyses from Bloomberg New Energy Finance, the levelized cost of green hydrogen could decrease by up to 80% by 2030 under favorable conditions, fundamentally altering the competitive landscape across multiple sectors.
Market scaling follows distinct trajectories across different hydrogen applications, with some reaching commercial viability more rapidly than others. Industrial applications where hydrogen directly replaces existing gray hydrogen streams typically represent the lowest-hanging fruit, showing positive economics with carbon prices as low as $50-70 per ton in many markets. Heavy transportation applications often follow, particularly in heavily-utilized fleet operations where operational advantages of rapid refueling and long range compensate for higher upfront costs. Power generation and residential applications generally require stronger policy support or higher carbon prices, though their role in providing seasonal energy storage and peak capacity becomes increasingly valuable in highly renewable energy systems.
Strategic investments across the hydrogen value chain are increasingly focused on developing optimized regional ecosystems rather than isolated projects. These integrated approaches coordinate investments in production, infrastructure, and end-use applications to create mutually reinforcing market developments. By concentrating initial deployments in industrial clusters with multiple potential hydrogen offtakers, developers can achieve earlier economies of scale while minimizing infrastructure costs. According to the Hydrogen Council, approaching market development through such coordinated clusters could reduce the total investment required for hydrogen market activation by approximately 35% compared to fragmented deployments, substantially accelerating the pathway to self-sustaining market growth.
Levelized cost analysis: green hydrogen vs. grey hydrogen production economics
The economic competitiveness of green hydrogen versus conventional gray hydrogen represents a crucial metric for market adoption across industrial applications. Current levelized cost comparisons reflect a narrowing but still significant gap, with green hydrogen production costs typically ranging from $3-8/kg depending on regional electricity prices, utilization rates, and electrolyzer capital costs. In contrast, gray hydrogen produced from unabated natural gas generally costs $1-3/kg, with the lower end represented by regions with inexpensive gas supplies such as the Middle East and Russia, and the upper range found in gas-importing regions like Japan and Europe. This cost differential explains the continued dominance of fossil-based production, which currently accounts for over 95% of global hydrogen supply.
Several key variables drive the economics of green hydrogen production, with renewable electricity pricing and electrolyzer utilization rates being the most significant. In optimal locations with exceptionally low-cost solar or wind resources, electricity can now be procured at $20-30/MWh, approaching the threshold where green hydrogen becomes competitive even without additional policy support. Electrolyzer utilization rates similarly impact economics, with systems operating at 50% capacity factor facing nearly double the capital cost burden per kilogram compared to those achieving 90%+ utilization. This dynamic creates particularly favorable economics for installations co-located with industrial facilities that can provide consistent hydrogen demand patterns, enabling high utilization rates that minimize the impact of capital expenditures on overall production costs.
Looking forward, the cost trajectory for green hydrogen shows substantial ongoing improvement potential as electrolyzer manufacturing scales from hundreds of megawatts to tens of gigawatts annually. Industry learning curves indicate that electrolyzer capital costs could decline by 60-80% by 2030 as global manufacturing capacity expands, while continuing reductions in renewable electricity costs further enhance economic competitiveness. When combined with carbon pricing mechanisms that internalize the environmental costs of gray hydrogen production, which emits